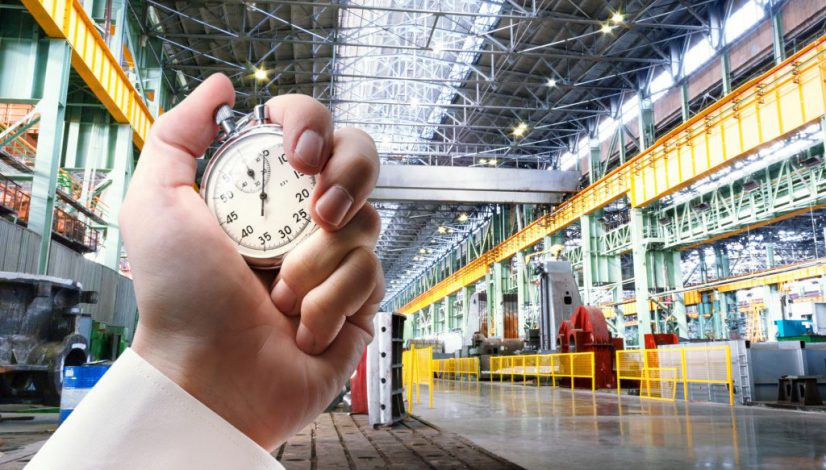
In the era of Industry 4.0, the Manufacturing Engineering and Operation Management divisions are increasingly committed to addressing critical issues of Material Handling: how can I move loads quickly and safely? Are there compact but flexible solutions? These are the most frequent questions that our team has found to answer.
The context and the problem
The evolution in companies of solutions and technologies necessary to manage the internal flows of materials, goods and/or finished products is incessant. The production processes have in fact undergone a radical transformation in industrial design thinking which has involved both internal goods handling systems and those related to storage.
The reason? The global market requires fast responses and an ever shorter time-to-market putting a strain on companies, which today find themselves experiencing an important challenge: offering customized products, increasing delivery speed and productivity, optimizing at the same time the costs, environmental impact and maximizing safety. As if that weren’t enough, another criticality is the high degree of customization in the production processes themselves: each context and each company formulate their choices in a unique way, generating a technological and process mix that is different each time, from case to case.
The eternal question between automation and flexibility, the evolution of handling equipment to achieve greater efficiency, increasingly tighter production processes to make the most of space and the need to pursue environmental sustainability objectives that guide all company strategies and construction of the building itself, push companies to rethink alternative ways of handling goods in order to remain competitive.
Our solution
Robik electric handlers fit perfectly into this context by meeting the new requirements in the Material Handling area: speed, safety, but with maximum flexibility, as well as a reduction in lead time and overall costs.
The Robiks impose new standards and multiple strengths: on the one hand they boast a compact structure and on the other hand they have an amazing lifting force up to 13.000 kg. They require the use of a single operator who, thanks to the radio control, can perform all the operations safely and with flexibility.
Multifunctional and modular
Robiks perform various functions, in fact they qualify as lifters, handlers, pushers, tows and electric tractors. In their various functions they have special equipment or in any case pluses that allow different uses according to the needs of the company, just think of the fact that they can be used inside or even outside the building.
Perfection and speed of movement even in tight areas
When positioning loads, the Robik lifts and carries the load vertically to an ideal position for maximum traction. The load to be transported is thus arranged above, but set back from the front traction axle. Thanks to this principle, we have been able to reduce the total length of the Robik making it particularly manageable, but with a large load capacity, improving running stability, reducing the dimensions and weight of the machine itself with the need for compensation by counterweights. The result? A solution also conceived as a shuttle / locomotive / electric tractor for towing trailers.
ROBIK moves the world
With Robik, the company will no longer have to design the layout of the processes and the production area based on the means of handling chosen, but it will be Robik himself who will adapt to the context in which he will have to move the materials, thus guaranteeing the company significant benefits in terms of quality, economy and efficiency in their business.